Quality management is particularly important for companies and manufacturers in the medical device industry. Since most of what they make will eventually use to save people’s lives, the quality of their medical devices can spell the difference between life and death for the patients. Medical device manufacturers are expected to make a conscious effort to continuously ensure the safety and quality of their products.
It can only be done if the manufacturer or maker has a sensible and sound quality management system (QMS) in place. If you’re looking for an RBC Medical device equipment manufacturer or similar devices, which emphasize quality control and excellent customer service, you might want to read on. Here are some quality management tips for those companies in the medical device industry:
1. Closely Monitor Design Control
Quality Management System (QMS) for the medical device industry starts with the design of the medical devices. You should put in place design controls that focus on both the science and engineering aspects of the patient’s needs.
The boundaries of medical research and medical technology will be constantly pushed forward by the state of science and technology. But the quality assurance team of a medical device manufacturing company should always make sure that the devices they make are designed in such a way as to take into account the convenience, comfort, safety, and pain or pressure tolerance of patients and customers.
For medical devices that have been released to the market, quality managers should seriously consider any customer feedback or complaints, if any. These should be taken into account in the succeeding versions or upgraded designs of the device.
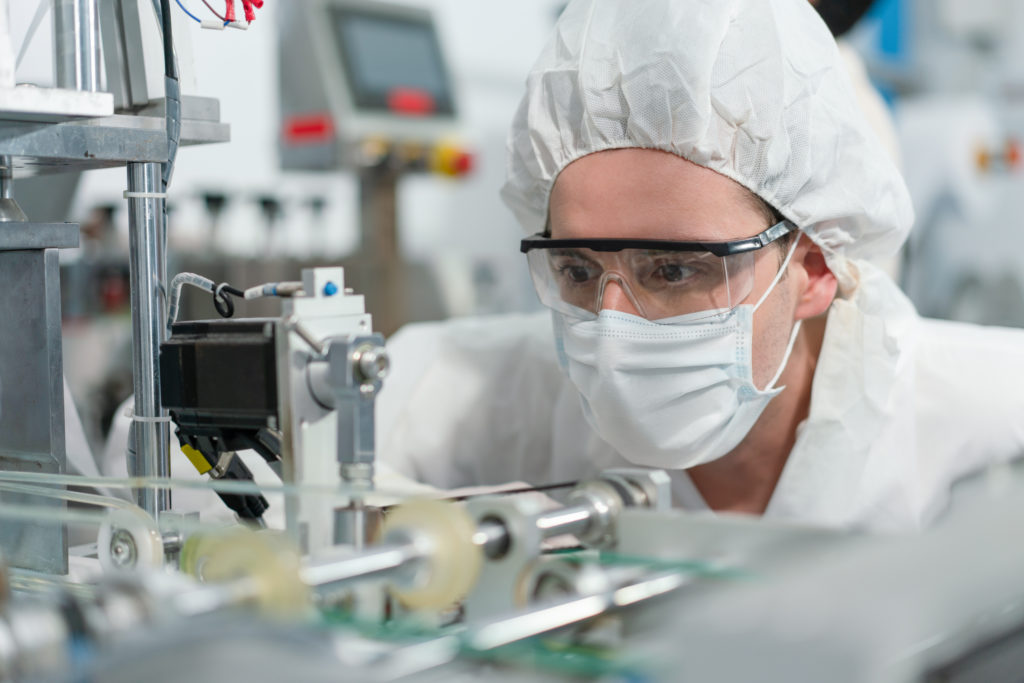
2. Set Quality As Benchmark Of All Roles And Functions
Executives and quality managers should align all teams with inputs and contributions to the quality management system and process with clear goals and expectations. It can’t be viewed as something that’s done and finished once the device leaves the manufacturing plant and gets boxed for delivery to distributors or sellers.
The leadership of the company, along with the quality managers, everyone who contributes to the design and manufacturing process, has to think of feedback and complaints from customers and patients as part of the quality management process throughout the product life-cycle. For example, collate feedback and complaints from customers actively, consider the design, innovation, and engineering process. You can do this by sending feedback request forms or conducting surveys among your clients and end-users.
You can create a team from your QMS department that will collate, study, and analyze the various feedbacks, comments, suggestions, and complaints from patients, customers, and medical practitioners. And see how these can be considered and fed into the device design. You don’t have to factor in every feedback or suggestion, but you should at least take the time to listen, especially to complaints which strike a common thread.
You should set clear expectations among your QMS teams. Emphasize that they need to maintain and constantly improve on quality. Ensure that excellence in quality is a core value to your objective that is observed in all of your quality assurance, design controls, and your whole QMS. Clearly define each team’s roles, the scope of responsibilities, and its members. Set the triggers and process for initiating a Corrective and Preventive Action (CAPA).
3. Use Audits As Valuable Feedback On Quality
Change the way you look at audits. Instead of thinking about audits as something your teams have to comply with or just a requirement you can meet with minimum compliance, you might want to reorient your teams to look at it as a valuable source of potential feedback about the work you do.
Under the Quality System Regulation (QSR) of the FDA, all manufacturers are required to have internal audits on quality as an ongoing concern. But instead of dreading and waiting for the quality audits, mobilize your teams to come up with an Action Plan on how you can design and implement your quality assurance procedures. You can use those quality audits as valuable feedback inputs.
4. Integrate Risk Management To QMS
Aside from the customer, or patient complaints about the discomforts, or inconveniences, which they might feel or experience from the use of your medical device, you should also pay attention to potential risks or reports of risk incidents from end-users. Risk management shouldn’t be limited to the pre-market phase. While your safety tests contribute a lot to improving the design, you should consider taking feedback from people who bought and used your device.
Their inputs should be looped and fed back into the design process. Any feedback or complaints from patients and end-users are the best data input and case studies to examine the potential risk of having defects. Quality control feedback can even drive product innovation.
For example, if an end-user complained of some harm experienced in using the device, you should take a closer look at it even if it seems to be an isolated incident. QMS teams should analyze whether the risks created or presented in using the device are due to the design itself or a defect from the manufacturing process.
Culture Of Quality
Manufacturing companies in the medical device industry are on the frontlines of a need for a culture of quality. With most of their products used in saving people’s lives, quality assurance should be a core value of their businesses. Most manufacturing companies in the medical device industry who were able to integrate risk management into their quality control systems were the highest-performing companies in the industry.